Overview and Objectives
Unsteady loading and the inability to confidently predict unsteady loading and / or quantify errors drives unnecessary redundancy and design conservatism.
Objectives
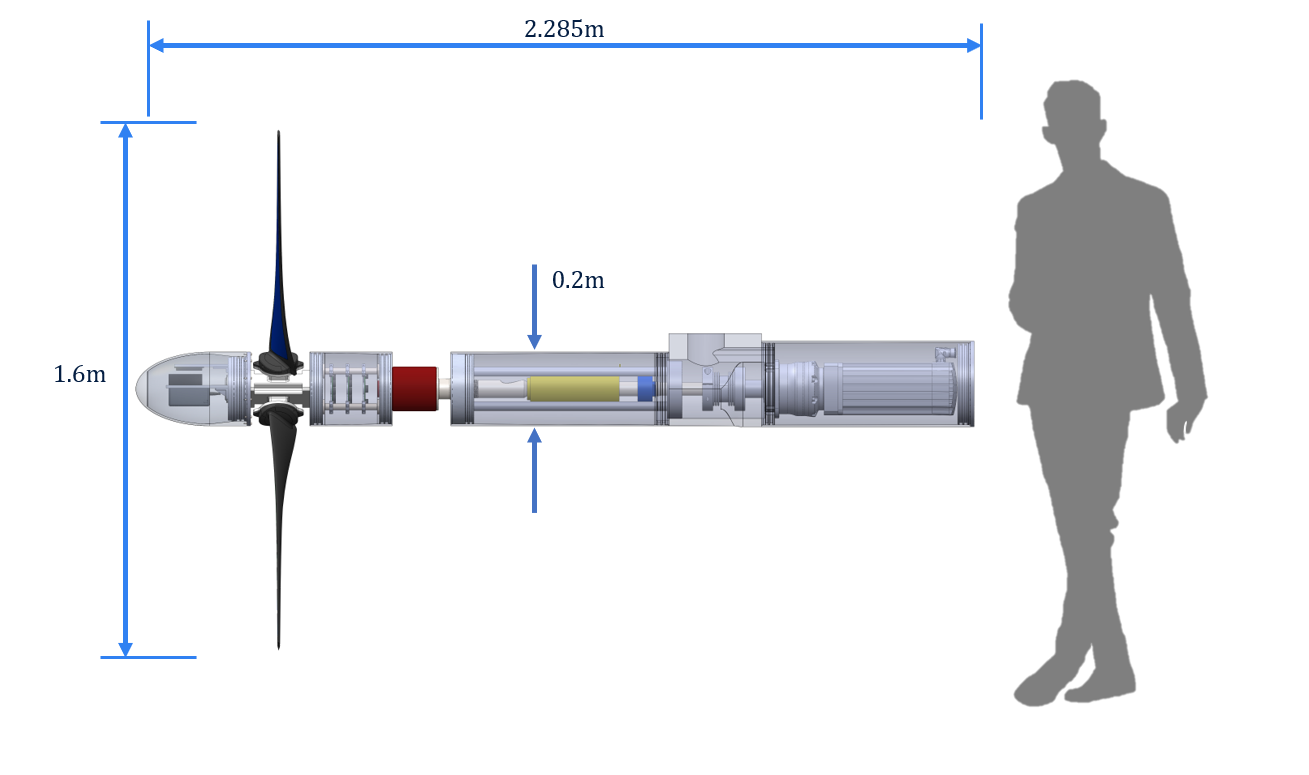
- improve accuracy of modelling techniques,
- improve confidence in the use of modelling techniques,
- quantify modelling errors for different techniques under different loading scenarios,
- development of novel measurement techniques.
Approach
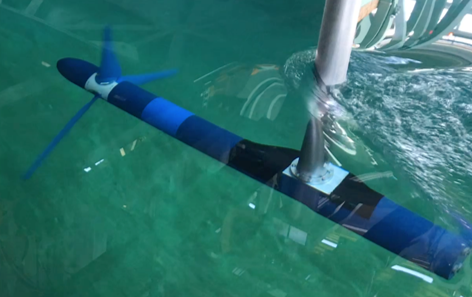
- Conduct a large laboratory test of a highly instrumented tidal turbine in waves and turbulent current to provide underlying data,
- Conduct a series of community wide (academia and industry) blind prediction exercises with staged data release, leading to an open access dataset.
Data Release and Example Submission Format
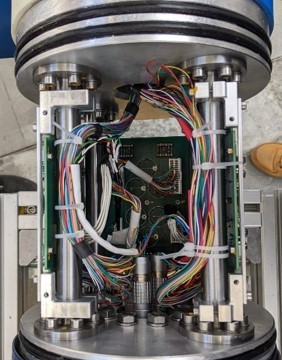
The data will be stage released through a series of workshops through which the community will be invited to participate in blind prediction exercises of different selected performance and unsteady loading cases.
- Stage 1 experiments have been conducted in April 2022, with 1st data release planned at a workshop on 2 November 2022.
- Stage 2 experiments are scheduled in late 2022 and data release in 2023.
- A blind prediction exercise will precede each staged data release.
Released Data Log
Data ID | Version | Description | Update Note | Link |
R_001 | 2 | Turbine and blade geometry, the benchmarking test cases and 2D CFD data for the blade hydrofoil profile. | R_001 link | |
Sub_001 | 2 | Example data submission for Stage 1 blind test | Sub_001 link |
Project resources
Presentation slides: Tidal Turbine Benchmarking Study opening workshop (30 June 2022)
Presentation slides: Tidal Turbine Benchmarking Study…
Video: Tidal Turbine Benchmarking Study opening workshop (30 June 2022)
Video: Tidal Turbine Benchmarking Study opening workshop…
Watch a recording of the Tidal Turbine Benchmarking Study Opening Workshop which took place on 30 June 2022.
Presentation slides: Tidal Turbine Benchmarking Study (EWTEC 2021 side event)
Presentation slides: Tidal Turbine Benchmarking Study…
Video: Tidal Turbine Benchmarking Study (EWTEC 2021 side event)
Video: Tidal Turbine Benchmarking Study (EWTEC 2021 side…
A recording on the Supergen ORE Hub side event at EWTEC 2021, which included the launch of the Unsteady Loading Tidal Turbine Benchmarking Study. To view the presentation about the study, please skip to 35 minites and 35 seconds.
FAQs
- How can you get involved in the Benchmarking study?
To register your interest in the tidal benchmarking project please email Xiaosheng Chen and include details of your modelling methodology in your email. - How can the data be accessed?
The data required for simulation setup, including turbine/blade geometry and benchmarking case conditions, can be accessed here. - How should the modelling data be formatted for submission?
The modelling data should be submitted in a folder structure containing tab-delimited text files for the actual simulation data and a .json file to contain the key details of the submission. An example data submission is available to download here in a .zip format. - What is the deadline for submitting data?
The current deadline for modelling data submission is 17 October 2022. There may be some limited flexibility in the submission deadline if you struggle to meet this date. Please contact Sam Tucker Harvey or Xiaosheng Chen to discuss if required. - Will uncertainty quantification be provided for the experimental data?
A detailed uncertainty quantification will be provided before the deadline for data submission to provide modellers with an indication of the level of uncertainty of the experimental data. - Will modellers be required to submit uncertainty quantification for modelling?
We would like modellers to include uncertainty quantification where possible, however it is appreciated that this will differ significantly depending on modelling methodology. - How is the trailing edge of the blade treated?
The blade profile is increased from the zero thickness of the sharp NACA 63-415 profile using a thickening function. This approach is used as 2D simulations performed in the blade design process demonstrated it to preserve the sharp profile performance much more closely than truncating the profile. This thickening is function is applied to maintain the non-dimensional profile constant along the blade span. - How was the instrumented blade developed and what is the design thinking behind it?
The design methodology of positioning the strain gauges/fibre Bragg sensors within an instrumentation channel inside the blades was driven by practical considerations regarding the large amount of wiring required for strain gauging. With all sensors within the blade, the design is more robust to the risks of instrumentation damage and leaks during the experimental campaign. - Will roughness measurements be provided for the turbine blade?
Roughness measurements are currently ongoing on one of the blades used in the test campaign using confocal microscopy. These measurements will be released to modellers when complete. - Will wind tunnel experiments be performed on a representative aerofoil section to validate the thickened and coated hydrofoil performances used for the turbine blades?
Wind tunnel experiments are currently being planned to create an experimental dataset with a representative roughness and coating thickness. This will be achieved by using the coating process and materials developed for the turbine blades. - What load measurements are provided by the benchmarking turbine?
The benchmarking turbine provides total rotor torque and thrust with the use of a torque/thrust transducer mounted to the rear end of the rotor. Additionally, root bending moments are measured within the hub for the edgewise and flapwise direction for each of the three blades. Finally, in-blade measurements provide by strain gauges in two blades, and fibre Bragg sensors in the third blade, provide the edgewise and flapwise bending moments at 5 locations within the blade.